低碳冶金研究所成立于2012年6月,研究所针对钢铁工业的“铁-煤”化工流程,其能源结构以煤为主,焦炭、电和原煤的能源消耗量占总能源消耗量的80%以上,钢铁工业实际上是典型的“碳”工业以及钢铁行业的高能耗、重污染、高消耗的特点,研究开发低碳冶金技术。2012年以来研究所在钢铁冶金新工艺新技术的开发,冶金炉渣高附加值循环利用,高品质钢的品种开发与质量控制以及物理场在冶金中的应用等方面承担过多项科研项目,取得了丰硕成果。先后承担过国家自然科学基金、安徽省重大科技攻关、广东省重大科技攻关、安徽省自然科学基金等项目,并与马钢、南钢、中天钢铁、韶钢、新余钢铁、梅钢等多家大中型钢铁企业建立了良好的合作关系。
研究所现有现有专职教师9人,其中教授3人、副教授4人,博士生导师3人、硕士生导师6人,1人入选安徽省学术与技术带头人。2022年团队获批安徽省高校优秀科研创新团队。
所 长: 范鼎东
副所长: 李杰
教师名单:
教授
范鼎东 李杰 夏云进
副教授
尹振兴 芮其宣 万勇 邓爱军
讲师
陶素芬 孙桂林
低碳冶金研究所-天生赢家凯发k8国际
传统钢铁工艺升级改造
钢铁冶金新工艺新技术的开发
炼钢过程智慧制造
冶金炉渣高附加值循环利用
高品质钢的品种与质量控制
(1)高效智能化炼钢关键技术
转炉炼钢的传统工艺是使用普通高炉铁水,为了脱硅、脱磷、脱硫需要加入大量的石灰而造成大量熔渣,大量熔渣吹炼带来金属收得率低、溶剂消耗高、冶炼时间长、粘枪及喷溅现象严重、热浪费等缺点;同时还由于钢包处理技术的在线应用和连铸生产的需要,要求较高的出钢温度而导致脱磷困难。而高效智能炼钢工艺通过减少渣量,降低铁耗,直接利用炼钢废弃物和氧化物熔融还原等核心技术和智能控制模型来指导转炉炼钢,可以显著提高转炉炼钢控制水平,降低企业生产成本,该技术获授权发明专利10余项、软件著作权1部、省部级二等奖2项,先后在马钢、中天钢铁、长江钢铁、山西鑫泰、天津钢铁等企业得到运用,降低成本超过5000万元/年。
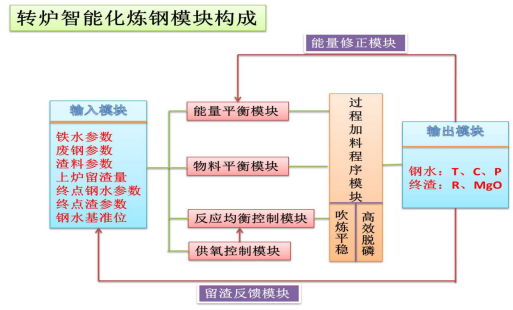
图1 智能炼钢构成
图2 智能模型及相关应用
(2)低温及超低温用钢研究与开发
低温钢是指适于在0℃ 以下应用的合金钢,能在-196℃以下使用的,称为深冷钢或超低温钢。低温用钢主要应具有如下的性能:(1)韧性—— 脆性转变温度低于使用温度;(2)满足设计要求的强度;(3)在使用温度下组织结构稳定;(4)良好的焊接性和加工成型性;(5)某些特殊用途还要求极低的磁导率、冷收缩率等。近年来,随着全球能源资源的多样化,以及对环境保护的日益重视,天然气作为一种清洁能源,将来占据的比重将越来越大。而我国天然气资源丰富但多集中于中、西部地区和海域,导致产地远离消耗区,引发运输和储存等相关技术问题。由于液态天然气储运温度在-162℃以下,要求用于储存液化天然气的材料在超低温下具有良好的低温韧性、强度、足够的抗脆性开裂和止裂能力。目前我国已建或在建的液化天然气储罐采用的均是双容罐,即由材质为含9%镍的镍钢板的内罐与材质为预应力混凝土的外罐双层罐体组成。而作为混凝土建筑结构主要增强材料的钢筋是hrb400、hrb500热轧带肋钢筋,其性能很难满足-162℃液态天然气低温储罐建造的要求,国内天然气低温储罐用钢筋完全依赖进口。研究所与南钢、韶关钢铁等共同开发了-165℃下使用的超低温钢筋,填补了国内空白。另外,同马钢共同开发了-50℃使用的风电法兰用钢,研究所在低温及超低温钢的研究开发方面具有比较丰富的实践经验。
图3 超低温钢的理论计算cct曲线
(3)冶金炉渣高附加值循环利用
钢铁生产的过程中会产生大量的冶金渣,如高炉渣、转炉渣、精炼渣、含铁尘泥、粉煤灰、铁合金渣等。2015年我国的粗钢产量约为8亿吨,冶金渣的产生量在4亿吨以上。据估算,每堆积1万吨废渣,约占地1亩。截止2015年,全国固体废物堆存量已超过100亿吨,占用和毁坏土地在300万亩以上,对我国已经很少的人均耕地构成严重的威胁。很多渣中含有大量碱性氧化物,可以侵蚀土壤致使土壤碱性化,严重地影响了土地的使用。另外,长期堆积固体废物,也会导致土壤中的重金属含量超标。许多冶金废渣中含有易溶于水的成分,在堆积过程中,经雨水的侵蚀,有害成分会随雨水和地表水流入江河湖海,有的被风吹入水中,或通过土壤渗入地下水,这就污染了堆积地区的水资源,从而危害附近居民的身体健康,甚至会危及原有的生态系统。钢渣在处理过程中,还会产生有害的气体和粉尘,以细粒状存在的废渣和其他废物会随风飘逸到很远的地方,造成大气的粉尘污染。此外,熔融态废渣的高温不合理利用,也会造成热辐射危害。另一方面,冶金废渣含有丰富的铁、钙、硅、铝、锰等元素,对其进行资源综合再利用的前景广阔。因此,研究冶金炉渣循环利用具有重要的现实意义,研究所与马钢积极合作,努力打造我国首个冶金渣综合利用示范基地。
图4 冶金渣渣企业内部综合利用技术路线图
(4)复合相(固液共存)炉渣脱磷新技术
脱磷是炼钢的主要任务之一,2022 年我国粗钢产量约为12亿吨,为了脱磷产生的炉渣约为12000 万吨(平均约为100kg/t 钢),消耗6000 万吨以上石灰,众所周知,炼钢用石灰是通过石灰石(不可再生资源)煅烧而成,其煅烧过程中会放出大量的co2,并且由于脱磷渣中存在着大量未反应的自由cao,炉渣很难回收利用,造成了极大的资源浪费。并且随着钢铁行业的飞速发展,世界范围内高品位优质铁矿石资源逐渐枯竭,以储量丰富、成本低廉的高磷铁矿为代表的低品位复杂铁矿资源的开发利用逐渐受到关注,高磷铁矿的使用必然会使铁水中磷含量增加,采用高磷铁水冶炼会加重炼钢脱磷负担,使石灰消耗与渣量进一步增加。因此,开发石灰消耗少、渣量少的脱磷技术至关重要。日本研究工作者从2006年开始研究固液共存炉渣脱磷技术,并约于2014年成功运用于工业实践,在实现高效脱磷的同时,大幅降低了石灰消耗及渣量。低碳冶金研究所从2012年开始研究复合相(固液共存)炉渣脱磷技术,取得了显著进展,并将该技术成功应用于低成本炼钢工艺中,为企业带来了显著的经济效益。
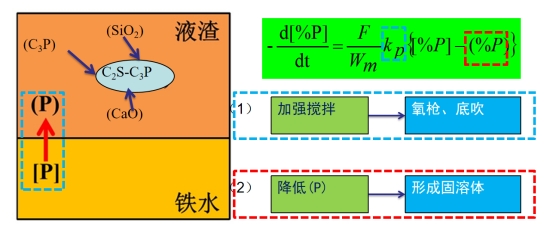
图5 复合相炉渣脱磷示意图
(5)精炼渣系控制与夹杂物控制模型开发
近年来,随着世界各国国防、轨道交通以及汽车等行业的快速发展和技术进步,对钢铁材料的使用性能要求越来越苛刻,为了满足客户对钢材质量越来越高的要求,不断提高钢水洁净度和合理控制钢中夹杂物类别、形态、大小与分布成为各个钢铁企业的重要任务,而作为提高钢水洁净度和钢中夹杂物控制水平的主要手段的钢包精炼越来越受到钢铁企业的重视,尤其是在特殊钢领域。团队根据不同钢的服役环境的不同,优化设计了精炼渣系,并建立精炼渣系控制与夹杂物控制模型,模型应用后实现了实现了碱度控制精度为±0.5的比例为92%,±0.7的比例为100%;cao/al2o3控制精度为±0.2的比例为90%,±0.3的比例为96%;
铝脱氧钢中b类夹杂物级别均≤1.0,d类夹杂物级别≤1.0的比例为100%,≤1.5的比例为98%;硅锰脱氧的弹簧钢中b类、d类夹杂物级别均≤1.0。
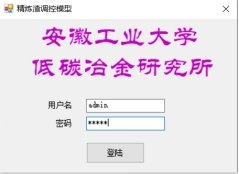
图6 精炼渣系控制模型
三、代表性科研项目
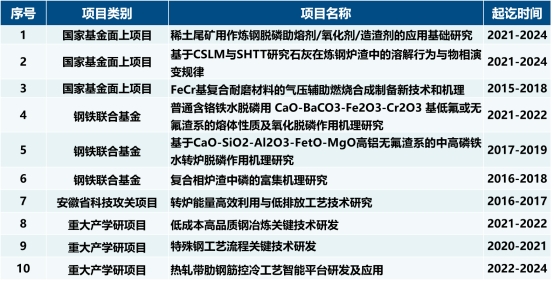
四、科研获奖